|
|
Konisch- oder flachdichtende
Verschraubungen gibt es für alle möglichen
Verbindungestechniken, so z. B. Gewinde-, Löt-, Klebe- und Pressverbindungen
und in allen Materialarten, so z. B. Messing, Rotguss, Edelstahl, Kunststoff.
> mehr |
|
Flanschverbindung |
|
Flansche
verbinden Rohrabschnitten untereinander. Auch Geräte, Armaturen und
Messgeräte mit größeren Nennweiten werden durch Flansche
mit den Rohren verbunden. Auch Wellrohre können mit flachdichtenden Flanschen verbunden werden. Flanschverbindungen unterliegen der Normung
nach DIN oder ANSI und werden nach Werkstoff, Nennweite, Lochbild und
der Nenndruckstufe unterschieden. >
mehr |
|
Gewindeverbindung |
|
Rohrgewinde werden in zwei verschiedene Abdichtungsarten unterschieden.
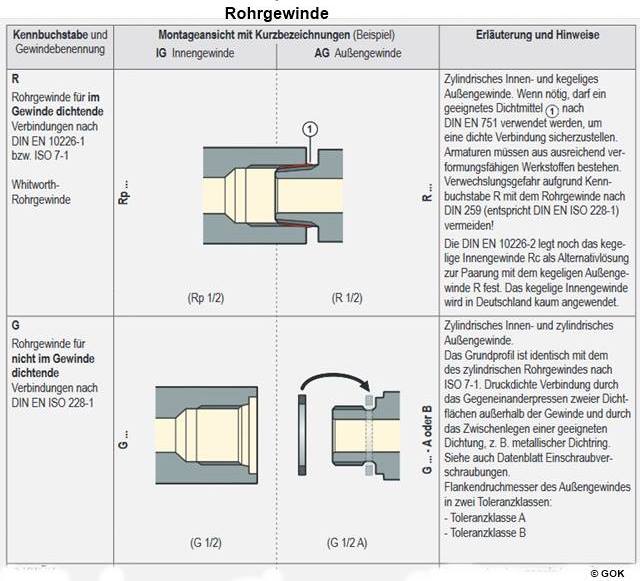
Quelle: GOK Regler- und Armaturen-Gesellschaft mbH & Co. KG
Das Rohrgewinde nach DIN EN 10226 "Rohrgewinde für im Gewinde dichtende
Verbindungen - Teil 1: Kegelige Außengewinde und zylindrische Innengewinde - Maße, Toleranzen und Bezeichnung" (frühere DIN 2999)
mit kegeligem Außengewinde (R) und zylindrischem Innengewinde (Rp) ist für eine
im Gewinde dichtende Verbindung ausgelegt. Um eine dichte Verbindung sicherzustellen, kann ein geeignetes
Dichtmittel (z. B. Hanf, Teflonband) im Gewinde verwendet werden. Das Rohrgewinde DIN EN 10226 ist auch als BSPT (British
Standard Pipe Taper) Whitworth-Rohrgewinde bekannt. |
|
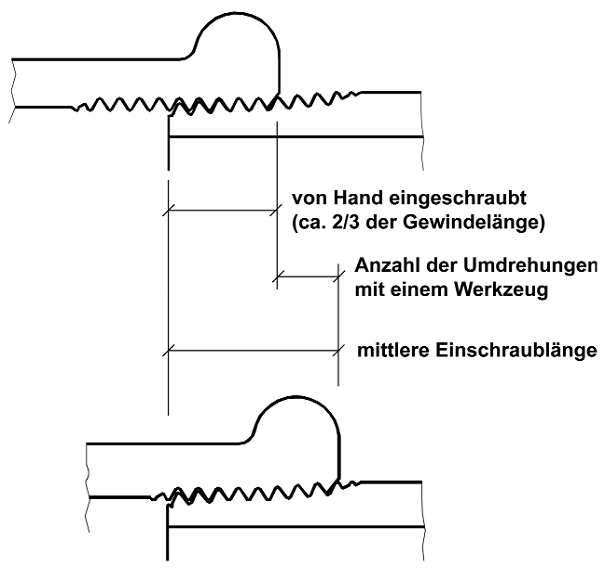 |
Quelle:
SANHA Kaimer GmbH & Co. KG |
|
Eine fachgerechte
Gewindeverbindung wird durch Gewinde nach EN 10226-1:2004-10
mit der Paarung R/Rp erreicht, wobei mit R das
konische Außengewinde (Kegel 1:16) und mit
Rp das parallele Innengewinde
bezeichnet werden. Dieses Gewinde ist auch in ISO 7/1 genormt.
Die Dichtwirkung wird theoretisch dadurch erzielt,
dass sich die Gewindeflanken des konischen Außen- und des
parallelen Innengewindes in einem durch die Fertigungstoleranzen
bestimmten Bereich berühren und somit eine metallische
Dichtung stattfindet. Zum Ausgleich von Oberflächenrauigkeiten
sowie zum Ausgleich von Fertigungstoleranzen (Flankenwinkel, Steigung)
wird ein zusätzliches Dichtmittel verwendet. Dies ist in der
klassischen Form Hanf als Dichtmittelträger,
der mit einem für die Trinkwasser- und Gasinstallation zugelassenen
Dichtmittel (wie z. B. neo-fermit) eingestrichen und geschmeidig
gemacht wird. Das Dichtmittel verhindert auch das
"Austrocknen" der Hohlräume und
somit das Eindringen von Wasser oder Feuchtigkeit. Dadurch können
die Teile nicht zusammenrosten (Spaltkorrosion). |
|
|
Das Rohrgewinde nach DIN EN ISO 228 "Rohrgewinde für nicht im Gewinde
dichtende Verbindungen - Teil 1: Maße, Toleranzen und Bezeichnung" (frühere Whitworth-Rohrgewindenormung DIN 259) Zylindrisches
Innen- und zylindrisches Außengewinde (G) ist für nicht im Gewinde dichtende Verbindung
ausgelegt. Das Gewinde wird hauptsächlich zur mechanischen Verbindung von Fittings und Armaturen eingesetzt.
Eine Abdichtung der Verbindung erfolgt durch das Gegeneinanderpressen zweier Dichtflächen außerhalb der Gewinde
und durch Einlegen einer geeigneten Dichtung. |
|
|
Das zylindrische Rp-Innengewinde DIN EN 10226 hat die gleichen
Nennmaße für die Gewindedurchmesser und das Gewindeprofil wie das zylindrische G-Innengewinde nach DIN ISO 228.
Aber das G-Innengewinde hat im Kern- und Flankendurchmesser nur positive Abmaße (bei der
DIN EN 10226 +/- Toleranz). Deshalb kann ein DIN EN 10226-kegliches Außengewinde in ein ISO 228-G-zyydrisches Innengewinde eingeschraubt werden,
jedoch lässt sich das Außengewinde ca. 1 Gewindegang weiter einschrauben und es entsteht aufgrund der großen Kerndurchmessertoleranz
beim G-Gewinde ein größerer Freiraum zwischen den Gewindespitzen und somit ein größerer
Leckpfad.
Ein zylndrisches G-Außengewinde sollte auf keinen Fall mit Rp-Innengewinde
kombiniert werden, da das Innengewinde zu eng sein kann. |
|
|
Klemmringverbindung |
|
Die Klemmverschraubung
wurde als Alternative zu den flach- oder konischdichtenden Verschraubungen
auf den Markt gebracht und besteht in der Regel aus drei Bestandteilen:
|
|
- Überwurfmutter
- Körper
- Dichtungs- bzw. Klemmring
|
|
Für Trinkwasser- und Gasinstallationen
müssen Klemmringverbindungen das DVGW- Prüfzeichen tragen! >
mehr |
|
Schneidringverbindung |
|
Schneidringverbindungen
können im Gegensatz zu den originalen Klemmverschraubungen bei Anwendungen
mit höherem Druck eingesetzt werden. Diese Verschraubungen bestehen
aus Überwurfmutter, Körper und Schneidring(en) mit einer scharfen
Kante, die in die Oberfläche des Rohrs eingreifen und dadurch einen
festen Halt erzeugen. >
mehr |
|
Rohrkupplung |
|
Eine Alternative zu konventionellen
Rohrverbindungstechniken für Kunststoff- und Metallrohre ist die
Rohrkupplung. Alle glattendigen Rohre können mit
wenigen Handgriffen verbunden werden. Die montagefertig angelieferte Kupplung
wird über die Rohrenden geschoben, ausgerichtet und in eine beliebige
radiale Montageposition gedreht. Ein wechselseitiger Anzug der beiden
Schrauben mit einem Drehmomentschlüssel gewährleistet eine sichere
Montage. Die Dichtzuverlässigkeit ist auch bei leichten Achsversätzen,
Auswinkelungen und sogar bei Rohrabständen bis zu 35 mm gewährleistet.
Auftretende Druckschläge, Vibrationen und Körperschall werden
deutlich gedämpft. >
mehr |
|
Steckverbindung |
|
Immer häufiger werden
Stecksysteme angeboten. Einige sind nachträglich
wieder lösbar. In der Praxis werden bevorzugt unlösbare Verbindungen
von den Fachbetrieben eingesetzt. Eigentlich sind auch nur unlösbare
Systeme zu tolerieren. >
mehr |
|
Manschettenverbindung |
|
Rohrkupplungen
können als Verbindungschellen
oder Dichtschellen (Reparaturschellen)
verwendet werden. Hierzu gibt es in verschiedenen Versionen (mit einem
Gelenk, einteilig oder zweiteilig, offen) für Heizungs-, Wasser-
und Abwasseranlagen. >
mehr |
|
Muffenverbindung |
|
Neue Rohrkupplung,
z. B. die Röhrs-Rohrkupplung, ist ein Kupplungselement
für steckbare Rohre, die überall dort besondere Vorteile aufweist,
wo besonders hohe Drücke auftreten. >
mehr |
|
Schnellkupplung
Schnellverschlusskupplungen bestehen aus Kunststoff, Messing, Aluminium, Stahl und
Edelstahl und werden für Pneumatik, Wasser- oder Öl-Hydraulik, Gase und sonstige Fluide eingesetzt. Sie werden in Nennweiten von 2 bis 300 mm
hergestellt und können mit Drücken von Vakuum bis zu 3.000 bar und können mit Temperaturen von niedriger als -253 °C bis über 800 °C
eingestzt werden. |
|
|
|
Schnellkupplungen ein-/beidseitig für Kältemittel-Leitungen |
Quelle: KTT - Klima Tech Tirol |
|
Ein Schnellkupplungssystem wird zu einer einfachen Installation von Klimaanlagen verwendet. Es bsteht aus einem entlüfteten Kupferrohr mit Schnellkupplungen und Gegenkupplungen für Innen und Außengerät. Die selbstdichtende Kupplungen sind für den dauerhaften Einsatz, dem wiederholten Koppeln und Entkoppeln ohne Evakuieren und zum neuen Befüllen der Komponenten geeignet. Auch das Evakuieren und/oder Vorbefüllen von Komponenten und Leitungen ist möglich.
. |
|
|
|
Diese Kupplungen
dürfen nach dem erfolgten Verschrauben nur noch von
einem Fachkundigen bzw. einem autorisierten Kundendienst
getrennt bzw. gelöst werden (Kältemittelverlust)! |
|
Einsatzbeispiele |
|
Beispiel 1: Die Anschlüsse
der Klimageräte sind mit unterschiedlichen, selbstdichtenden
Einfachkupplungen ausgerüstet. (Das Anschlussventil
am Außenteil des Klimagerätes verfügt über
eine Absperrvorrichtung, das Raumteil nicht.) Bei dem Anschluss
der Splitleitungen ist auf das Herstellen der korrekten
Verbindungen zu achten.
Bei der kältetechnischen Verbindung muss zuerst zwischen
dem Raumgerät und den Splitleitungen und erst dann
zwischen Splitleitungen und Außenteil hergestellen
werden. Bei der Verwendung eigener Kälteleitungen (ohne
Kältekupplungen) ist diese Reihenfolge ebenfalls einzuhalten!
Die Splitleitungen (Gas- und Flüssigkeitsleitung bzw.
Saug- und Druckleitung) haben jeweils eine Einfachkupplungshälfte "männlich" und eine Einfachkupplungshälfte
"weiblich", die über einen Schraderventilanschluss
verfügt.
In Kombination mit den an den Splitgeräten bereits
vorinstallierten Kupplungshälften ist ein fehlerhafter
Anschluss der Splitleitungen (sofern die richtigen Splitleitungen
verwendet werden) ausgeschlossen, da jeweils immer nur eine
Kombination aus zwei passenden Kupplungshälften zur
Verfügung steht. Splitleitungen mit gleichen Abmessungen
(Kupplungsgröße) können über ihre Kupplungen
aneinandergereiht und so bis zu einer max. Länge von
20 m verlängert werden. Quelle: Glen Dimplex
Deutschland GmbH |
|
Vorgefüllte
Kältemittelleitungen mit Schnellkupplungen |
Quelle:
REMKO GmbH & Co. KG |
|
|
|
Beispiel 2: Die Leitungen sind bei einseitigen Schnellverschlüssen an einer Seite fix mit
den Bördelanschlüssen des Innengerätes verbunden u. werden in der gewünschten Länge, aufgerollt am Innengerät hängend, geliefert.
Dadurch werden die Schnellkupplungen am Innengerät eingespart. Diese Variante reduziert die Kosten für die Schnellkupplungen.
Am freien Ende der Leitungen befinden sich die Schnellkupplungen, von denen die weiblichen Hälften bereits am Außengerät aufgeschraubt
sind. Maximale Leitungslänge 10 m.
Bei kompliziertem Leitungsverlauf und großer Leitungslänge empfielt sich die Verwendung von beidseitigen Schnellverschlüssen.
Bei beidseitigen Schnellverschlüssen wird die Kältemittelleitung samt den männlichen Schnellverschlusshälften getrennt vom
Innengerät geliefert. Die weiblichen Schnellverschlusshälften befinden sich bereits am Außen- und Innengerät. Maximale Leitungslänge 20 m, gestückelte Rohre mit
beliebiger Länge lieferbar. |
|
|
Kältemittel-Doppelrohr mit Schnellkupplungen ein-/beidseitig |
Quelle: KTT - Klima Tech Tirol |
|
Vorteile:
• Industriell gefertigte Verbindungen schließen Fehler bei der Montage aus und gewährleisten eine hohe
Zuverlässigkeit sowie minimale Leckageraten.
• sparen Zeit und technische Ausrüstung bei der Montage von Neuanlagen
• verhindern den oft vollständigen Kältemittelverlust bei unsachgemäßer Demontage durch nicht zertifizierte
Personen oder Unternehmen
• ermöglichen ohne aufwendige Ausrüstung einen einfachen und zeitsparenden Standortwechsel bei
minimierten Kältemittelverlusten
Nachteile:
• Die Abdichtung erfolgt in der Schnellkupplung durch einen O-Ring. Daher sind Schnellverschlüsse weniger
zuverlässig als fachgerecht hergestellte Bördelverbindungen.
• Die Erstinbetriebnahme kann durch den Kunden erfolgen, eine spätere Übersiedlung darf laut Gesetz nur
durch einen dafür zertifizierte Fachmann erfolgen.
Quelle: KTT - Klima Tech Tirol |
|
|
|
|
Da lösbare
Verbindungen (Verschraubungen, Langewinde) durch Verwindungen
und thermischen Beanspruchungen undicht werden können, dürfen
sie nicht verdeckt bzw. "unter Putz"
und nicht für die Erdverlegung verwendet werden,
ggf. sind Revisionsöffnungen vorzusehen (nach DIN
18380 [VOB Teil C] müssen alle unter Putz liegenden lösbaren
Verbindungen zugänglich bleiben - Neu - "Lösbare
Verbindungen, deren Dichtheit nicht dauerhaft sichergestellt ist, müssen
zugänglich sein"). Sie müssen mit dem jeweilig notwendigen
Werkzeug zugänglich sein. Ob eine Verbindung
(z. B. Verschraubung, Steckverbindung) als "unlösbare"
Verbindung eingestuft ist, muss aus den jeweiligen Herstellerangaben
entnommen werden. Gegebenenfalls ist eine
Revisionsöffnung zu setzen, damit man mit dem geeigneten Werkzeug
(teilweise Spezialwerkzeuge) arbeiten kann. |
|
|
|
|
KNIPEX Cobra® Hightech-Wasserpumpenzange |
|
|
Quelle: KNIPEX-Werk · C. Gustav Putsch KG |
|
Wasserpumpenzange
Die Wasserpumpenzange ist ein Werkzeug, das in jeder Tasche bzw. Werkzeugkasten eines Anlagenmechanikers
für Sanitär-, Heizungs- und Klimatechnik (Heizungs- und Lüftungsbauer, Gas- und Wasserinstallateut) vorhanden ist. Da die Zange, fachgerecht eingesetzt,
für viele verschiedende Arbeiten eingesetzt werden kann, ist sie der verbreitetste Zangentyp, die in verschiedenen Größen (100, 125, 180, 250 und 300 mm)
angeboten wird. Die Greifzange mit einem verstellbarem Gleitgelenk hat unterschiedlich große Öffnungsweiten des Mauls
zum Greifen und Festhalten unterschiedlich großer Werkstücke (Rohre, Muffen, Flachmaterial) und Bearbeiten von Schrauben/Muttern verschiedener Arten sowie mit Schutzeinlagen auch Armaturen.
Auch wenn die Greifbacken der Wasserpumpenzange in der Regel verzahnt sind, ist sie keine Rohrzange,
weil sie sich von dieser bauartbedingt eindeutig unterscheidet. Oft wird die WaPu-Zange als Allround-Werkzeug angesehen und nicht bedacht, dass
die zu bearbeitenden Teile beschädigt werden. Dies passiert besonders bei Armaturen und Schrauben (zerkratzen) bzw. bei Fittings (zusammendrücken). Zusätzlich können noch Schonbacken aufgesetzt werden. Hier sind dann aber der Einsatz von Zangenschlüssel oder passende Rohrzangen sinnvoll bzw.
fachlich richtig. |
KNIPEX Cobra®, Hightech-Wasserpumpenzangen - KNIPEX-Werk · C. Gustav Putsch KG |
|
|
|
|
|
|
Zangenschlüssel mit paralleler Gleitführung
|
|
|
Quelle: KNIPEX-Werk · C. Gustav Putsch KG |
|
Zangenschlüssel
Der Zangenschlüssel ist für bestimmte Arbeiten eine fachlich richtige Alternative zur Wasserpumpenzange. Er ist eine Kombination aus Verstellschlüssel und Greifzange mit verstellbarer
Maulweite und glatten Greifbacken. Die Greifbacken des Zangenschlüssels sind in jeder Zangenstellung annähernd parallel geführt.
Die abgebildete Zangen erreichen durch eine Linearführung der Backen in jeder Stellung eine gute Parallelität und können
über eine entsprechend angepasste Verstellmöglichkeit die Backen bei den notwenigen Maulweiten ebenfalls parallel an den
Kanten des Werkstücks anlegen und eignen sich besonders als Armaturenzange.
Je nach Größe des Zangenschlüssels (125, 150, 180, 200, 250, 300 mm) können Muttern, Schraubenköpfe, Armaturen- und Verschraubungssechskant mit größeren Durchmessern gegriffen werden und ersetzen dadurch eine größere Anzahl von Schraubenschlüssel mit unterschiedlichen Maulweite. Der aufzubringende Drehmoment wird durch die Länge der Griffe der Zange erreicht bzw. begrenzt. Mit den glatten und parallel geführten Greifbacken lassen sich
Werkstücke mit parallelen Kanten wie die verchromten Überwurfmuttern von Armaturen schonend greifen. Zusätzlich können noch Schonbacken aufgesetzt werden. |
Zangenschlüssel, Zange und Schraubenschlüssel in einem Werkzeug - KNIPEX-Werk · C. Gustav Putsch KG
.
. |
|
|
|
|
|
Armaturenmontage - Werkzeuge
Für die Montage und zum Auswechseln von Armaturen sind die richtigen,
vor allen Dingen geeigneten, Werkzeuge eine Voraussetzung. Schrauben, Verschraubungen und
Sechskantbauteile besonders an Sanitärarmaturen mit empfindlichen Oberflächen
(verchromt) sollten nicht das Allroundwerkzeug "Pumpenzange" kennenlernen. Zum Festhalten und Anschrauben von
Armaturen jeder Art sollten Zangenschlüssel und/oder Armaturenschlüssel die erst
Wahl sein. Für Standarmaturen wird man ohne einen Standhahnmutterschlüssel nicht zurechtkommen und
für das Festziehen und Lösen von Siphonverschraubungen gibt es Siphonzangen.
Im Internet gibt es
viele mehr oder weniger gute Einbau- und Sanierungsvideos. Besser ist es, wenn man sich an die Einbauanleitungen der Hersteller hält. |
|
|
|
Quelle: KNIPEX-Werk · C. Gustav Putsch KG |
|
|
Armaturenzange / Armaturenschlüssel
|
Quelle: SANPRO® GmbH |
|
|
|
Quelle: KNIPEX-Werk · C. Gustav Putsch KG |
|
|
|
|
|
|
|
Schweißverbindung
(Autogenschweißen) |
|
Bei dem Schweißen von Stahlrohren, Flanschen und Blechen wird zwischen
dem Nachlinksschweißen (Linksschweißen <3 mm Rohrwand-/Blechdicke)
und Nachrechtsschweißen (Rechtsschweißen >3 mm Rohrwand-/Blechdicke)
unterschieden. Das Autogenschweißen wird eingesetzt, wenn die Schweißnähte
schlecht zugänglich sind, also vor Ort auf der Baustelle und in allen
Lagen, unter bestimmten Umständen auch mit einem Spiegel (Linksschweißen).
An diesen Stellen ist in der Regel ein Schweißen mit einem E-Schweiß-
oder Schutzgashandstück nicht möglich. |
|
Leider wird des Autogenschweißen in vielen Betrieben nicht
mehr angewendet, weil die Kosten des Schweißens
relativ hoch sind, eine erhöhte Gefahrenlage beim Gasschweißen vorhanden ist und auch die heutige Ausbildungspläne im SHK-Handwerk die früher üblichen Schweißkurse nicht mehr vorsehen. Außerdem gibt es immer neue Rohrverbindungstechniken.
In der Praxis gibt es Probleme, wenn in den Aufträgen (z. B. Fernheizungen, Rohrleitungsbau) das Autogenschweißen gefordert wird. Hier fehlen oft die Monteure mit den entsprechenden Schweißberechtigungen (gültige Schweißpässe). |
|
Beim Gasschmelzschweißen (Autogenschweißen oder Acetylenschweißen) wird das Metall
mittels offener Flamme, die bei der Verbrennung von Ethin (C2H2 - Acetylen) und Sauerstoff (O2) entsteht, erhitzt und direkt oder durch
Zugabe von speziell legiertem Schweißdraht miteinander
verbunden.Die Schweißgase werden auch bei dem
Brennschneiden eingesetzt. > hier geht es weiter |
|
|
|
Schweißverbindung
(Kunststoffrohr) |
|
PVC-,
PE-, PB- und PP-Rohr
(Thermoplaste) können mit Spezialwerkzeugen
verscheißt werden. In Großanlagen wird das
Warmgasschweißen (Heißluftschweißen)
eingesetzt. Hier unterscheidet man zwischen dem Fächelschweißen
(der Schweißstab wird von Hand geführt) und dem Ziehschweißen
(Extrusionsschweißen > der Schweißzusatz
wird über eine Ziehdüse zur Schweißfuge geführt).
In der Haustechnik kommt das Heizelementschweißen
zum Einsatz. Die Kunststoffrohre werden ohne
Zusatzwerkstoff gefügt, wobei die Erwärmung
durch den direkten Kontakt mit der Wärmequelle
erfolgt. Dabei darf das Material nicht überhitzt werden, weil es
sich sonst zersetzt. Der Schweißvorgang besteht aus zwei
Arbeitsschritten. Erst wird der Rohrwerkstoff an der Fügestelle
erwärmt und dann mit einem festgelegten Fügedruck verbunden.
Man unterscheidet drei
Heizelementschweißen Polyfusions-Schweißverfahren: |
|
|
- Heizelement-Muffenschweißen
Die Rohrenden müssen gereinigt
und mit einem Spezialwerkzeug mit einer Fase versehen
werden. Das Schweißgerät ist mit einem
beheizten teflonbeschichteten Schweißdorn bzw. einer Schweißmuffe
einem zur Rohrweite passendem Durchmessers ausgerüstet. Nachdem
die Schweißtemperatur am Gerät erreicht ist wird das
Rohrende und das Muffenende auf das Schweißgerät gesteckt,
nach einer genau vorgegebenen Zeit aufgeschmolzen und beide Teile
(Schweißmuffe und Rohr) sofort zusammengepresst. Dabei entsteht
eine einwandfreie, dichte Verbindung. Wichtig ist, dass die Temperaturen
und die Aufwärmzeiten nicht überschritten werden. Auch
darf bei der Verschweißung im Inneren des Rohrquerschnittes
kein Wulst auftreten, der den freien Rohrquerschnitt erheblich verringert.
Dieses Verfahren muss sehr sorgfältig und unter günstigen
Bedingungen ausgeführt werden.
|
|
|
|
Heizelementstumpfschweißen
(Spiegelschweißen) |
|
Heizelement-Schweißmaschine |
Quelle:
ROTHENBERGER Werkzeuge GmbH |
|
- Heizelementstumpfschweißen
Die gereinigten und entgrateten planabgetrennten
Rohrenden werden gleichzeitig und gegenüberliegend an einem
Heizelement (Spiegel) unter Druck erwärmt und plastifiziert.
Dabei muss darauf geachtet werden, dass sich am Umfang der Rohrenden
gleichmäßig große Wulste bileden, deren Höhe
vom Rohrwerkstoff, von der Temperatur und dem Fügedruck abhängt.
Wenn die Temperatureinstellwerte zu hoch eingestellt sind, dann
führt das zu unerwünscht hoher Wulstbildung, was sich
besonders negativ auf den Innenquerschnitt des Rohres auswirkt.
Nach Ablauf der nach
dem Material vorgegebenen Anwärmzeit werden
die beiden Rohrenden abgenommen und so lange zusammengedrückt
gehalten, bis die Schweißnaht erstarrt und
abgekühlt ist. Die Kunststoffrohre können
bis zu einer Nennweite von DN 32 von Hand gefügt
werden. Ab einer Nennweite von DN 40 müssen
die Verbindungen mit Schweißmaschinen hergestellt
werden, da aufgrund des vorgegebenen Fügedrucks und wegen des
Fließ- und Fügeverhaltens der Thermoplaste bis zu einer
genau festgelegten Höhe aufgebaut und während der gesamten
Abkühlzeit konstant gehalten werden. Nur so sind qualitativ
hochwertige Stumpfschweißnähte für Druckleitungen
möglich.
Da sich bei PVC-Schweißverbindungen nicht eingehaltene Schweißeinstellwerte
sehr negativ auf die Schweißnahtgüte und Druckleitungen
aus PVC bei ungünstigen Baustellen- und Montagebedingungen
auswirken, werden diese Rohre hauptsächlich geklebt.
Die Heizelement-Schweißmaschinen sind mit
geeigneten Trenn-, Halte- und
Anpress-Vorrichtungen ausgestattet, die einen kontrollierten
Schweißvorgang gewährleisten. Hier sind auch die vom
Hersteller angegebenen Einstellwerte einstellbar.
Grundwissen
zum Schweißen von Polyethylen
|
|
|
|
Arbeitsablauf |
|
Heizwendelschweißgerät |
Quelle:
ROTHENBERGER Werkzeuge GmbH |
|
-
Heizwendelschweißen
Kunststoffrohre aus PE-HD und
PB in der Gas- und Wasserversorgung
werden hauptsächlich durch Heizwendelschweißen
verbunden. Dieses Verfahren ist inzwischen so weit automatisiert,
dass Rohr- und werkstoffspezifische Daten über Strichcodes
oder Magnetkarten eingelesen oder über codierte Anschlüsse
am Heizwendelfitting durch die Stromkabel auf das Schweißgerät
übertragen werden. Der Schweißvorgang läuft automatisch
ab.
Die zur Plastifizierung (Aufschmelzung) der Fügestelle
in der Muffe und an den Rohrenden findet durch in den Fitting eingebetteten
Heizdrähte. Bei der Stromzufuhr wird das Material auf ca. 220
bis 280 °C (materialabhängig) erhitzt und dadurch aufgeschmolzen.
Der notwendige Fügedruck wird durch die Wärmeausdehnung
des erhitzten Kunststoffes erreicht. Dies setzt eine spezielle Haltevorrichtung
oder Rohrfixierung voraus, damit es zwischen den Rohrenden und dem
Heizwendelfitting keine axialen Ausweichbewegungen gibt.
Das Heizwendelschweißen muss besonders sorgfältig
durchgeführt werden, damit die Verbindung dauerhaft dicht ist.
Die Rohrenden müssen staub-
und fettfrei gemacht und teilweise mit speziellem
Rohrschälwerkzeug am Umfang abgeschält werden. Auch die
Schweißfittings mit den integrierten Anschlussbuchsen sollten
erst unmittelbar vor dem Schweißen aus ihrer Verpackung genommen
und die inneren Fügeflächen dabei nicht berührt werden.
Die Verbindungsflächen müssen vollkommen fett- und staubfrei
sein und bleiben.
Die Herstellerangaben sind unbedingt
einzuhalten, damit Erwärmung und Fügedruck ausreichen.
|
|
|
Warmgasschweißen
(Heißluftschweißen)
Das Warmgaschweißen ist heutzutage
ein Heißluftschweißen, da das Schweißgerät
nicht mehr mit Gas sondern elektrisch beheizt wird, was eine bessere Temperatureinstellung
ermöglicht.
Das Schweißen von Thermoplasten
erfordert folgende Arbeitsgänge:
• Vorbereiten der Schweißflächen
• Erwärmen der Schweißzonen
• Zusammenfügen der Teile unter gleichzeitigem Aufbringen des
Schweißdrucks
• Abkühlen der Schweißnaht unter Aufrechterhalten des
Drucks
• Entlasten des geschweißten Materials vom Druck
• Nacharbeit der Schweißnaht |
|
Fächelschweißen
Die Fächelschweißmethode
wird nur noch selten angewendet und kommt nur an
schlecht zugänglichen Stellen und engen Radien zum Einsatz.
Außerdem ist die das Schweißverfahren langsam und erfordert
einige Übung.
Beim Warmgasschweißen werden die zu verbindenden
Flächen und der Schweißstab
gleichzeitig mit Warmluft auf Schweißtemperatur
erwärmt und unter Druck verschweißt. Dabei tritt die
Warmluft aus einer Runddüse
am Warmgasschweißgeräts aus, das mit einer Hand unter
senkrechten Pendelschwingungen (Fächelbewegungen)
geführt wird, während mit der anderen Hand der Schweißzusatzwerkstoff
zugeführt wird.
Das Warmgasschweißen wird für den Bau von Behältern,
Kanälen, Schächten, Rinnen, Auskleidungen und Fußbodenbelägen
angewendet. Aber auch das Verbinden von Kunststoffrohren für
Abluft, Trinkwasser, Abwasser und thermoplastischen Profilen (Dachrinnen
und Fensterprofile) sind Anwendungsfälle.
|
|
Fächelschweißen
eines Rohrabzweiges aus PVC hart. |
Quelle:
DVS e. V. |
|
|
|
Ziehschweißen
- Extrusionsschweißen
|
|
|
Ziehschweißen
Quelle: DVS e. V. |
|
Extrusionsschweißen
- Extruder |
Quelle:
IKS |
|
Im Gegensatz zum
Fächelschweißen wird der Schweißzusatzwerkstoff
bei dem Zieh- und Extrusionsschweißen
"maschinell" der Naht zugeführt.
Bei dem Ziehschweißen
wird der Scheißzusatz durch ein Führungsrohr
in der Heißluftdüse (Warmgasdüse)
geführt. Die Heißluft erwärmt den Schweißzusatz
und das Grundmaterial und plastifiziert beide Materialien.
Der plastifizierte Schweißzusatz wird durch die Düsenzunge
auf das Grundmaterial gedrückt. Bei dickwandigen Kunststoffteilen
können mehrere Schweißlagen notwendig werden. Durch dieses
Verfahren ist eine schnelle Schweißung möglich.
Das Extrusionsschweißen
wird hauptsächlich zum Schweißen dickwandiger
Kunststoffteile (Behälterbau) eingesetzt. Hier ist
in der Regel nur eine Schweißlage notwendig. Der Grundwerkstoff
wird von der Heißluft vorgewärmt und der Zusatzwerkstoff
wird in plastifizierter Form zugeführt. Dabei wird er mit Hilfe
eines Schweißschuhs in die Naht eingepresst.
Merkmale des Extrusionsschweißen:
- Es wird mit einem art- und formmassegleichen Schweißzusatz
geschweißt.
- Der Schweißzusatz ist homogen und vollständig plastifiziert.
- Die Fügeflächen werden mit Warmluft auf Schweißtemperatur
erwärmt.
- Die Plastifiziertiefe beträgt 0,5– 1,0 mm.
- Die extrudierte Masse wird mit einem Schweißschuh verteilt
und angedrückt.
- Es wird eine hohe Nahtgüte und mit niedrigen Eigenspannungen
sowie kürzere Arbeitszeiten und höhere Festigkeitswerte
erreicht.
Extrusionsschweißen
- IKS Kunststoff- und Stahlverarbeitungs GmbH |
|
|
|
|
Lötverbindung |
|
Das Löten
ist ein thermisches Verfahren zum stoffschlüssigen
Fügen von Metallen, durch das Schmelzen
eines Lotes (Schmelzlöten) oder durch die Diffusion
an den Grenzflächen der Werkstoffe (Diffusionslöten).
Die Lötverbindungen sind nicht lösbare, stoffschlüssige
und elektrisch leitende Verbindungen, die mit einer schmelzbaren
Metalllegierung (Lot) hergestellt werden. > mehr |
|
Je nach Branchen und Anwendungen unterscheidet
man verschiedene Lötverfahren > mehr |
|
|
|
|
|
Klebeverbindung
Das Kleben wird heutzutage zunehmend in
allen Bereichen der Technik als anerkanntes Fügeverfahren
eingesetzt. Besonders im Automobil- und Flugzeugbau wird diese Fügetechnik
eingesetzt, weil dadurch eine erheblich Gewichtsminderung erreicht wird.
Weltweit werden ca. 250.000 verschiedene Klebstoffe verwendet.
Deswegen muss ein Klebstoff besonders genau für seine konkrete Aufgabe
ausgewählen werden.
Mit Klebeverbindungen können bei fachgerechter
Ausführung nahezu alle Werkstoffe in allen
möglichen Kombinationen langzeitbeständig miteinander verbunden
werden. Die DIN EN 923 definiert ein Klebstoff als ein
Nichtmetall und ein Bindemittel, das
über Adhäsion und Kohäsion
wirkt. Die Verbindungen sind im Gegensatz zum Schweißen oder Löten
wärmearm und eine Schwächung
der Fügeteile wie beim Nieten oder Schrauben findet nicht statt.
> mehr |
|
|
|
Pressverbindung
Die Pressfittigverbindung ist eine kraftschlüssige
Verbindung, die durch das Verpressen gegen auseinanderziehen gesichert
ist. Die Abdichtung zwischen Rohr und Fitting erfolgt
durch werkseitig in Nuten der Fittingmuffe oder des Fittingstutzens ein-
bzw. aufgelegte O-Ringe. Ein DVGW-Prüfzeichen ist
für Trinkwasser-, Gas- und Flüssiggasinstallationen forderlich.
Für Gasinstallation oder Solaranlagen
müssen Pressfittings mit speziellen Dichtelementen
versehen sein. Presssystem für Solaranlagen mit O-Ring sowohl aus EPDM (Temperatur bis zu +120 °C, Dampf kompatibel) oder speziell füe Anwendung im Solarbereich mit grünem Zeichen (Temperaturen bis zu +180 °C bzw. +200 °C (nach Herstellerangaben), aber nicht mit Dampf kompatibel).
Dichtungswerkstoffe für Solaranlagen |
|
|
|
|
Pressfittingsystem
- Arbeitsablauf
Quelle: Deutsches Kupferinstitut
e.V. |
|
Einsatzbereiche:
- Trinkwasser (kalt und warm)
- Heizung bis 110 °C
- Kühlwasserleitungen
- Sprinkleranlagen
- Regenwasser
- Solaranlagen
- Gasanlagen
- Inerte Gase
- Feuerlöschanlagen
- Druckluft bis 16 bar, ölfrei
Der empfohlene Ablauf
des Verpressens ist:
Kontrolle der richtigen Einstecktiefe, um sicherzustellen,
dass das Rohr bei der Vormontage nicht versehentlich aus den Formstücken
herausgezogen wurde und eine sichere Verpressung möglich
ist.
Zange so ansetzen, dass die Sicke der Muffe in
der mittigen Aussparung des Werkzeuges ist und nach der Bedienungsanleitung
des Herstellers die Verpressung ausführen.
Verpressungen systematisch in einer selbstgewählten
Reihenfolge (z. B. in Fließrichtung des Wassers) durchführen,
um sicherzustellen, dass alle Muffen aller Formteile verpresst
wurden. (Hinweis: Beim Abdrücken der Leitungen können
u. U. auch unverpresste Verbindungen bei einem Prüfdruck von
16 bar noch dicht sein, jedoch später im bestimmungsgemäßen
Betrieb bei Druckstößen im System undicht werden oder
vom Rohr gedrückt werden!)
Prüfen der vollständigen und ordnungsgemäßen
Verpressung.
Die Arbeitsgänge
beim Pressen
1. Entgraten, weiche
Rohre kalibrieren
2. Einstecktiefe markieren
3. Sitz des Dichtelementes prüfen
4. Fitting bzw. Rohr unter leichtem Drehen auf- bzw. einschieben
5. Pressbacke auswählen, aufsetzen und Pressvorgang auslösen
6. Verpresste Verbindungen kennzeichnen
Rohrleitungssysteme mit Pressfittings für alle Anwendungen - SANHA GmbH & Co. K |
|
|
|
Mit dem Pressverbindungssystem
"Megapress" können auch dickwandige
Stahlrohre (DIN EN 10220 [alt > DIN 2448 - Siederohr],
DIN EN 10255 [alt > DIN 2440 / 2441 - mittelschwere und schwere
Gewinderohre]) mit Pressfittings verbunden
werden.
Die Megapress-Fittings
sind aus Zink-Nickel-beschichtetem Stahl gefertigt
und in den Dimensionen DN 15 bis DN 50 lieferbar. Für die
Haltekraft der Verbinder sorgt der integrierte Schneidring.
Die Dichtheit nach dem Verpressen garantiert ein spezielles
Profil-Dichtelement aus EPDM,
das sogar die unebene Oberfläche eines lackierten Stahlrohres
ausgleicht. Verarbeitet werden die Fittings mit Viega Presswerkzeugen
in Kombination mit abgestimmten Pressbacken und Pressringen.
Die SC-Contur der Viega Fittings stellt darüber hinaus
sicher, dass bereits bei der Dichtheitsprüfung versehentlich
nicht verpresste Verbindungen auffallen.
Megapress-Verbindung
|
|
|
Neben dem Hartlöten und Schweißen kann auch bei Kupferrohr die Presstechnik eingesetzt werden. Bei der Presstechnik entfällt der Arbeitsschritt des Formierens, da bei dieser kalten Verbindungstechnik keine Zunderbildung auftritt.
Das Verpressen von Trinkwasser-, Heizungs-, Gas- und CO2-Rohren wird schon seit Jahrzehnten mit hoher Präzision und langer Haltbarkeit durchgeführt. Inzwischen wird auch die Presstechnik im Bereich der Kälte- und Klimatechnik eingesetzt. Das Problem war, stabile, dichte Pressverbindungen, die langfristig abdichten, hohen Betriebdrücken standhalten und für Kältemittel geeignet sind, herzustellen. Hier wurden speziell aufeinander abgestimmte Fittings, Dichtringe und Presswerkzeuge, die auch die besonderen Anforderungen an Temperaturbeständigkeit und Ölfestigkeit erfüllen, entwickelt. |
|
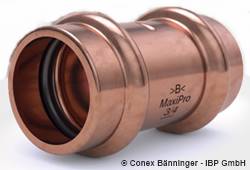
Presssystem >B< MaxiPro
Quelle: Conex Bänninger - IBP GmbH
|
Ein Beispiel ist das Presssystem >B< MaxiPro® zur Herstellung dauerhaft dichter, sicherer Rohrverbindungen in der Kälte-Klimatechnik, das speziell für Anwendungen bis 48 bar Betriebsdruck entwickelt wurde.
>B< MaxiPro ist ausschließlich durch geschulte und zertifizierte (>B< MaxiPro Training) Fachhandwerker zu verarbeiten. Alle Anlagen sind gemäß der gesetzlichen Vorgaben und den allgemein anerkannten Regeln des Kälteanlagenbauerhandwerks unter Beachtung der lokalen Unfallverhütungsvorschriften zu installieren. |
|
|
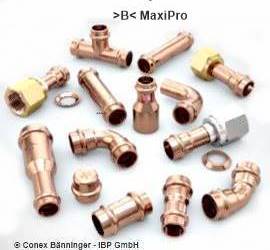
Presssystem >B< MaxiPro
Quelle: Conex Bänninger - IBP GmbH
|
Vor der Verarbeitung ist zu prüfen, ob Rohr, Fitting und Pressebacke die richtige Größe haben.
Fittings und Rohre müssen sauber und frei von Verschmutzungen sein, der O-Ring darf keine Beschädigungen aufweisen und die Profile sind zu prüfen. Grundbacken und Wechseleinsätze müssen frei von Verschmutzungen sein. Pressverbindungen sollten ausschließlich an nicht unter mechanischer Spannung stehenden Rohren vorgenommen werden.
• Die Verbindung ist hergestellt, sobald der Pressvorgang gestartet und vollständig beendet wurde.
• Pressen Sie nicht mehrfach den gleichen Fitting.
• Nach der Verpressung sollte die Verbindung nicht verdreht werden.
Quelle: Conex Bänninger - IBP GmbH. |
|
|
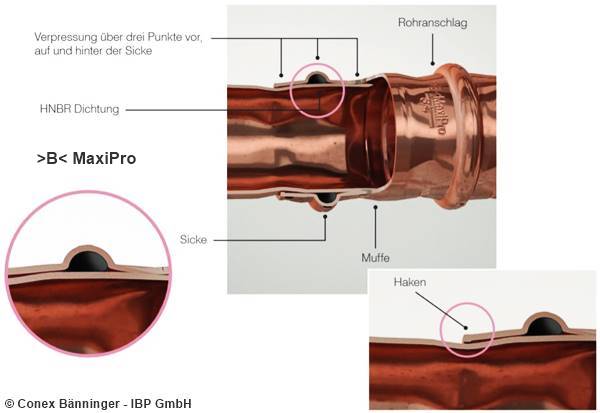
Durch eine Verpressung vor, auf und hinter der O-Ring-Sicke wird mit >B< MaxiPro eine dauerhaft dichte, kraftschlüssige Verbindung hergestellt.
|
|
Wenn in der Nähe von Pressverbindungen Hartlötungen notwendig sind, so müssen Mindestabstände eingehalten werden, damit das Dichtelement nicht durch Hitzeeinwirkung beschädigt wird. Hier sind die vom Hersteller angegebenen Maße einzuhalten. Die in der Praxis bekannten Abhilfemaßnahmen zur Kühlung des Pressfittings (z. B. Kühlung mit feuchtem Lappen, Kühlspray) sollten möglichst vermieden werden. |
|
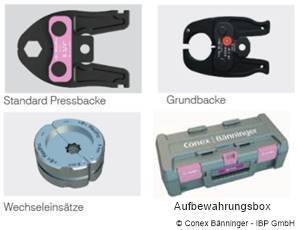
Pressbacken >B< MaxiPro
Quelle: Conex Bänninger - IBP GmbH
|
Einsatz und Tausch von Wechseleinsätzen:
• Entfernen Sie immer die Pressbacke aus dem Presswerkzeug, bevor Sie den Einsatz wechseln.
• Die Einsätze bestehen aus zwei Teilen (Paar) und sind mit einer Nut versehen, sodass sie seitlich in die Backe ge- schoben werden können. Ein gefederter Haltestift sichert den Einsatz in der Backe.
• Die Nut stellt sicher, dass beide Wechseleinsätze korrekt eingesetzt werden.
• Wählen Sie die richtige Größe des Wechseleinsatzes für den zu verpressenden Fitting und stellen Sie sicher, dass
beide Teile des Einsatzes die gleiche Grösse haben.
• Setzen Sie den ersten Teil des Einsatzes von der Seite in die Grundbacke ein. Achten Sie darauf, dass der Einsatz auf der entsprechenden Nut sitzt und der Punkt auf dem Einsatz in Richtung Backenöffnung zeigt. Sie spüren ein Klicken, sobald der Haltestift einrastet.
• Wiederholen Sie den Vorgang mit dem zweiten Teil des Einsatzes.
• Um die Wechseleinsätze zu entfernen, drücken Sie bitte die beiden Knöpfe an der Backenöffnung (je ein Knopf auf einer Seite der Grundbacke). Bei Betätigung der Knöpfe lösen sich die Einsätze aus der Grundbacke.
ACHTUNG: Bitte lassen Sie die Einsätze nicht aus großer Höhe fallen.
• Bewahren Sie die Wechseleinsätze immer in der entsprechenden Verpackung auf.
Quelle: Conex Bänninger - IBP GmbH |
|
|
Die Press-Revolution - >B< MaxiPro
Conex Bänninger - IBP GmbH |
|
Conex Bänninger empfiehlt die Verwendung von ROTHENBERGER 19 kN Presswerkzeugen.
• Für zöllige Fittings werden Standardbacken verwendet. 19 kN Presswerkzeuge können Fittings bis zu einer Größe von 1 1/8" verpressen. Für Fittings größerer Abmessungen, muss ein 32 kN Presswerkzeug mit entsprechender Pressbacke ver wendet werden.
• Für metrische Fittings wird eine Grundbacke mit austauschbaren Wechseleinsätzen verwendet. 19 kN Presswerkzeuge können Fittings bis zu einer Größe von 28 mm verpressen.
|
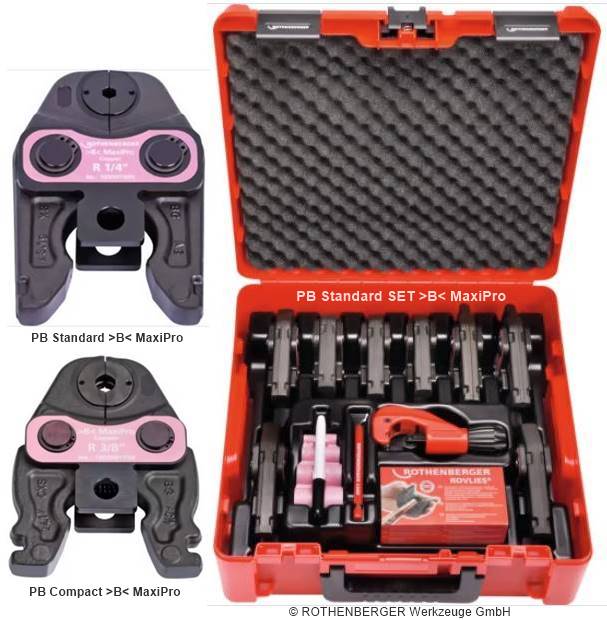
PB Standard SET >B< MaxiPro 1/4"-1.1/8" -
Pressbacken PB Standard >B< MaxiPro 1/4" und Compact >B< Maxi Pro 1/4"
|
|
|
|
|
Einpressanschluss |
|
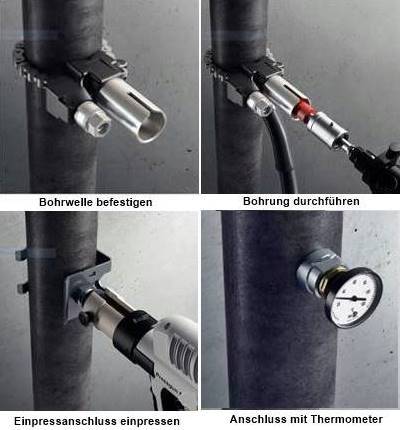
Herstellung eines Einpressanschlusses
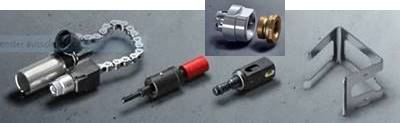
Werkzeugset für den Einpressanschluss - Bohrführung, Bohrwelle, Pressmaschineneinsatz, Positionierungshilfe, Einpressanschluss Rp 3/4 - Innengewinde und Reduzierstück auf ein Rp 1/2 - Innengewinde
Quelle: Viega GmbH & Co. KG
|
|
Immer weniger Heizungsbauer können Autogenschweißen oder es ist zu aufwendig, einfache Anschlüsse für Thermometeter, Manometer, Temperaturfühler, Entleerungs- bzw. Spüleinrichtungen oder Leitungsanschlüsse an dickwandigen Stahlrohren (DN 40 bis DN 150) herzustellen. Hier bietet sich die Presstechnik an.
Mit einer geeigneten Pressmaschine und einer handelsüblichen Bohrmaschine können Einpressanschlüsse hergestellt werden.
Arbeitsschritte
1 Eine spezielle Bohrvorrichtung zur Führung der Bohrwelle wird am Stahlrohr befestigt.
2 Bohrung mit der Bohrmachine durchführen und die Bohrvorichtung wieder abnehmen. An der Bohrvorrichtung kann ein Industriestaubsauger befestigt werden, sodass bei der Bohrung anfallende Späne direkt abgesaugt werden können.
3 Einpressanschluss mithilfe des Pressmaschineneinsatzes in das Rohr einpressen.
4 Fertig ist der Stahlrohr-Anschluss für die nachträgliche Installation von Thermometern, Temperaturfühlern, Manometern, Entleerungs- bzw. Spüleinrichtungen oder Leitungsanschlüssen.
Serienmäßig hat der Einpressanschluss ein Rp 3/4-Innengewinde und ein Reduzierstück auf ein Rp 1/2-Innengewinde ist lieferbar. |
|
|
|
|
|
|
Schiebehülsenverbindung |
|
|
Schiebehülsen-Fitting |
Quelle:
aquatherm GmbH |
|
Die Schiebehülsentechnik
(SHT) ist eine besondere Art zur Herstellung einer unlösbaren
Verbindung (form- und stoffschlüssige Verbindungsart)
mit Mehrschicht-Metallverbund-Rohr, PB-
und Pe-Rohr. Sie wird in den Abmessungsbereichen
von 12 bis 110 mm eingesetzt. Je nach Hersteller sind die
Messingfittings für die Einsatzmöglichkeiten Trinkwasser,
Heizung, Gas und Druckluft
zertifiziert und zugelassen. |
Eine dauerhaft
dichte Verbindung entsteht durch das Verpressen
einer Schiebehülse über das Rohr mit dem Fitting.
Die Schiebehülsenverbindungstechnik darf nur
mit den von den Systemherstellern angebotenen Rohren,
Werkzeugen, Form- und Verbindungsteilen genutzt werden. |
|
|
|
Schiebehülsenverbindung |
Quelle:
aquatherm GmbH |
|
|
|
|
Herstellen
einer Schiebehülsenverbindung bei dem
Rehau-System mit dem RAUTITAN©-Rohr
Quelle: REHAU Industries SE & Co. KG
RAUTOOL_Montagewerkzeuge |
.
FASTLOC - Sicher verbinden ohne Aufweiten
Quelle: REHAU Industries SE & Co. KG
|
Beim Verpressen drückt die Schiebehülse das Rohr über die Innenhülse gegen den Fitting-Grundkörper und das Rohrmaterial nimmt die Form der Fittingkontur an. Somit ist die Verbindung ohne zusätzlichen O-Ring dicht.
Einfach schnell. FASTLOC
REHAU Industries SE & Co. KG
Einfach schneller fertig: FASTLOC ist ohne O-Ring dicht
HaustechnikDialogNews |
|
|
|
|
|
|
|
|
|
Hinweis! Schutzrechtsverletzung:
Falls Sie meinen, dass von meiner Website aus Ihre Schutzrechte verletzt
werden, bitte ich Sie, zur Vermeidung eines unnötigen Rechtsstreites,
mich
umgehend bereits im Vorfeld zu kontaktieren, damit zügig
Abhilfe geschaffen werden kann. Bitte nehmen Sie zur Kenntnis: Das zeitauf-wändigere
Einschalten eines Anwaltes zur Erstellung einer für den Diensteanbieter
kostenpflichtigen Abmahnung entspricht nicht dessen wirklichen oder mutmaßlichen
Willen. Die Kostennote einer anwaltlichen Abmah-nung ohne vorhergehende
Kontaktaufnahme mit mir wird daher im Sinne der Schadensminderungspflicht
als unbegründet zurückgewiesen. |
|
|
|
Videos aus der SHK-Branche |
SHK-Lexikon |
|
|



| |